Green Hydrogen: A Multibillion-Dollar Energy Boondoggle
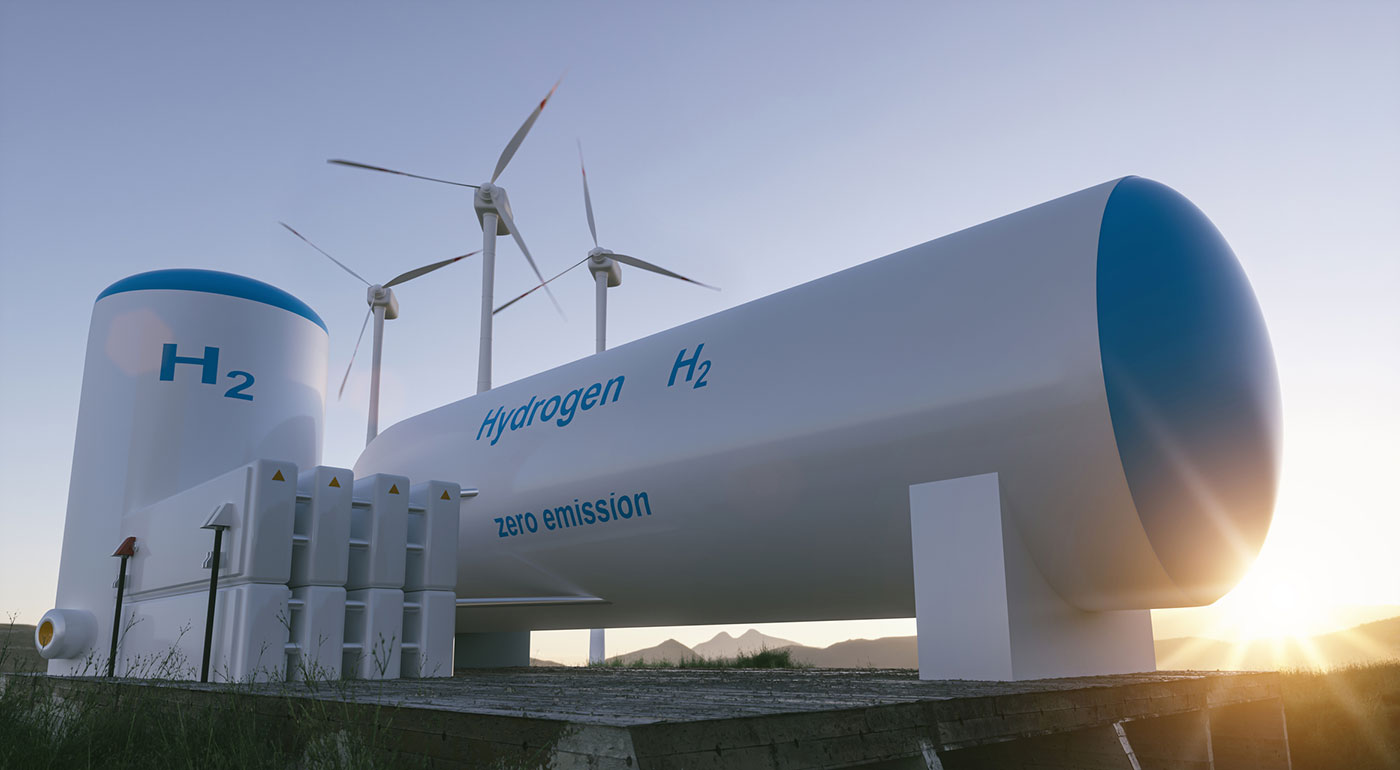
Introduction
This past October, the Biden administration announced $7 billion in subsidies to create seven Regional Clean Hydrogen Hubs. In addition, under the 2022 Inflation Reduction Act (IRA), green hydrogen—hydrogen manufactured with no carbon emissions—will be eligible for a production tax credit of up to $3 per kilogram (kg) produced. These subsidies are part of the administration’s Clean Hydrogen Strategy, which calls for manufacturing 10 million metric tons of green hydrogen per year by 2030 that will be used to reduce carbon dioxide (CO2) emissions from “hard-to-decarbonize” industries by 25 million metric tons annually.[1] The administration’s Hydrogen “Earthshot” program,[2] launched in 2021, calls for producing green hydrogen at an average cost of just $1 per kg by 2030, via two distinct processes: electrolysis, using “surplus” wind and solar power; and reforming methane and capturing the resulting CO2 (both processes are explained below).
As this Issue Brief will explain, the Clean Hydrogen Strategy and the accompanying tax credits are a multibillion-dollar energy boondoggle that is unlikely to be achieved and, even if it is achieved, will have no measurable impact on climate. The high cost of the production tax credit—$3/kg is equivalent to $91 per megawatt-hour (MWh), based on the energy content of hydrogen—is far greater than wholesale electricity prices in the U.S., which in 2023 averaged between $30/MWh and $50/MWh.
The key problem with using hydrogen as an “energy carrier” is that, unlike coal or natural gas, hydrogen cannot be extracted directly in elemental form and then used. Instead, hydrogen, like electricity, must be manufactured. And in contrast to crude oil that must be refined into usable products like gasoline and diesel fuel, more energy is required to manufacture hydrogen than that hydrogen contains. No technology can change this immutable thermodynamic fact. Consequently, and in contrast to fossil fuels and nuclear power, hydrogen’s “energy return on investment” (EROI), i.e., the ratio of energy output to energy input, is less than one. Coupled with the additional lost energy from combusting (burning) hydrogen directly or using it in a fuel cell, hydrogen’s overall energy efficiency is dismal, making its use as a primary energy carrier self-defeating.
There are two potential reasons to use hydrogen as an energy resource: (1) it is carbon-free when combusted in pure oxygen (burning hydrogen in air produces oxides of nitrogen [NOx]); and (2) it can be used as an energy storage medium (such as a battery or hydroelectric dam). However, in terms of mitigating climate change, the administration’s goal of reducing CO2 emissions by 25 million metric tons per year represents less than two days’ of total energy-related U.S. CO2 emissions in 2022 and less than six hours of world CO2 emissions in 2022. Hence, the Clean Hydrogen Strategy will have no measurable impact on world climate. Moreover, the costs of manufacturing green hydrogen relative to the resulting CO2 reductions from the use of fossil fuels result in an avoided cost far greater than current values for the so-called social cost of carbon (SCC)—i.e., the dollar estimate of the economic damage resulting from the emission of a ton of carbon dioxide into the atmosphere.
Hydrogen may be useful for long-term energy storage as an alternative to batteries. However, the increased need for stored energy to ensure reliable supplies of electricity is itself an artifact of government mandates to electrify fossil-fuel end uses, especially vehicles, and replace the generation of electricity by fossil fuels primarily with intermittent wind and solar electricity.
For those concerned about increasing the availability of zero-emissions energy, nuclear power—especially, small, modular reactors—represents a more fruitful and potentially cost-effective source, if some of the existing barriers would be removed.[3] Moreover, an increased reliance on nuclear power would avoid the need to increase energy storage.
Ultimately, the announced subsidies for clean hydrogen hubs and the hydrogen production tax credits in IRA are just the latest in almost a half-century of giveaways for ill-conceived energy projects that benefit favored constituents at the expense of economic rationality.
The Quest for an Energy “Holy Grail”
The search to find a virtually unlimited supply of clean, low-cost, and reliable energy is nothing new. In the 1950s, some claimed that nuclear fission would be the answer. More recently, proponents of nuclear fusion claim that it will fulfill the promise, although it remains decades away from commercialization and has remained so for decades.
The current holy grail of energy is hydrogen, the most abundant element in the known universe. When burned in the presence of pure oxygen, hydrogen’s only by-product is water. Moreover, the supply of hydrogen supplies is virtually limitless if it is extracted from seawater. So in their pursuit to reduce carbon emissions, politicians and policymakers are increasingly looking to “green” hydrogen—hydrogen whose production does not release any carbon emissions. The intent is to use green hydrogen instead of fossil fuels in industrial applications, as a replacement for transportation fuels and to generate emissions-free electricity whenever it is needed, using Dispatchable Emissions-Free Resources (DEFRs)—i.e., electricity that is not intermittent (such as wind or solar power) but always available on demand. Practically speaking, this will mean electricity-generating turbines that burn hydrogen rather than natural gas or petroleum.[4]
The fundamental problem with using hydrogen as an energy resource,“green” or otherwise, is that it cannot be extracted directly in elemental form.[5] Today, almost all hydrogen is manufactured by “steam methane reforming,”[6] which uses high-temperature steam in the presence of a methane source, such as natural gas, to release hydrogen. The problem? This process releases far more CO2 than simply burning natural gas directly.[7] However, the hydrogen produced today is used almost exclusively not as an energy carrier but as a feedstock—as a raw material to fuel petroleum refining and the manufacture of ammonia.[8]
The other current method to manufacture hydrogen is electrolysis.[9] This involves running an electric current through water.[10] Today, little hydrogen is manufactured via electrolysis because it is far more costly to do so than by reforming natural gas. Moreover, unless the electricity used is generated from zero-emissions resources, electrolysis is not emissions-free.
To encourage the production of green hydrogen and further the U.S. toward a zero-carbon future, the Biden administration has established several programs. Crucially, the 2021 Hydrogen “Earthshot” program aims to reduce the cost of manufacturing green hydrogen via methane reforming with carbon capture, or electrolysis, to just $1 per kilogram by 2030. But $1/kg is about 80% less than the $5/kg current cost of hydrogen produced by electrolysis.[11] By contrast, it costs $1.00–$1.50/kg to manufacture hydrogen by reforming natural gas without carbon capture, depending, of course, on the cost of the natural gas itself.
The administration also introduced a production tax credit to subsidize green hydrogen production as part of the 2022 Inflation Reduction Act (IRA). Under IRA, green hydrogen is eligible for a tax credit of up to $3/kg.[12] Most recently, in October 2023, the administration announced $7 billion earmarked to create seven green hydrogen manufacturing hubs throughout the country, with a goal of producing 10 million metric tons of green hydrogen annually by 2030.[13] Several of the hubs will manufacture hydrogen via electrolysis using wind and solar electricity, while others will do so by methane reforming using natural gas but supposedly will capture and sequester the resulting CO2 emissions.[14]
As the remainder of this Issue Brief discusses, the prospects for manufacturing low-cost, emissions-free hydrogen by 2030 are unrealistic, barring major technological breakthroughs and their commercialization.[15] Even if such breakthroughs do occur, the physical realities—and cost—to produce, transport, and store hydrogen make it inherently uneconomic as an energy carrier.
Hydrogen Is a Net-Energy Loser
A fundamental reality of harnessing energy for productive uses—such as transportation, heating and cooling, and lighting—is that doing so requires energy. For example, petroleum must be extracted, refined, and transported, which requires energy. Nuclear power requires mining uranium and processing it into usable fuel. Then there is the energy needed to manufacture furnaces, motors, and turbines that generate electricity. Next, there is the energy lost when fossil-fuel plants (and nuclear reactors) generate electricity and losses when electricity is transmitted and distributed to its final end use.
Absent environmental concerns, the most desirable sources of energy are those that produce the most energy output for the least amount of energy input.[16] (Dispatchability—the availability of an energy resource when it is needed—is another important attribute.) The ratio between the amount of energy required to create a usable energy resource and the amount of energy that the resource provides is called the “energy return on investment” (EROI). EROI is similar in concept to a financial return on investment, except that instead of measuring returns in dollars, one uses measures of energy, such as joules or British thermal units (Btus). (Those measures also can be converted into kilowatt-hour [kWh] equivalents.)[17]
One kilogram of hydrogen (approximately 2.2 pounds) contains the equivalent energy of just under 40 kWh of electricity, although some of that energy is lost when hydrogen is combusted. This is known as the “higher heating value” (HHV),[18] and it measures the maximum theoretical amount of energy that can be captured when hydrogen is combusted. However, manufacturing hydrogen entails additional energy losses. Hydrogen proponents claim that electrolyzers, which split water molecules into hydrogen and oxygen atoms, will use electricity supplied by surplus wind and solar generation to produce zero-emissions hydrogen. But electrolyzers are, at most, 80% efficient, meaning that at least 20% of the energy, i.e., the electricity, used is lost in the manufacturing process.[19]
At 80% efficiency, it takes at least 49 kWh of delivered electricity to produce 1 kg of hydrogen.[20] (At 70% efficiency, an electrolyzer would require 57 kWh/kg.) Electric transmission and distribution system losses, such as from distant wind and solar facilities to hydrogen manufacturing facilities, mean that another 3%–5% more electricity must be generated, depending on transmission distance. After hydrogen is manufactured, it must be compressed, so that it can be stored and transported. Typically, hydrogen is pressurized to 350 or 700 bar (a metric measure of pressure; 1 bar is slightly less than normal atmospheric pressure) or liquefied. Compression to 700 bar, for example, requires between 5% and 15% of hydrogen’s HHV, or between 2 kWh/kg and 6 kWh/kg.[21]
Hence—ignoring the energy required to manufacture the materials needed for an electrolyzer plant itself, as well as the energy used to construct and maintain an electrolysis facility, including compressors—a simple and conservative EROI value can be derived (Table 1).
Table 1
Derivation of Direct EROI for Hydrogen (H2) Production by Electrolysis
Line No. | Energy Input per kg of H2 in kWh | |
1 | Transmission and Distribution of Electricty from Electric Generating Resource | 1.5–2.5 |
2 | Electrolysis per kg of H2 Manufactured | 49–57 |
3 | Compression per kg of H2 | 2–6 |
4 | Total Energy Input per kg of H2 | 52.5–65.5 |
5 | Useful Energy Output per kg of H2 (Lower Heating Value)* | 33.4 |
6 | EROI (5) / (4) | 0.51–0.64 |
As shown in Table 1, the useful energy contained in hydrogen that is produced via electrolysis is, at best, just over 60% of the energy required to manufacture it. This contrasts with other dispatchable fossil fuels and nuclear power, which all have EROIs greater than one, even after including the energy consumed to manufacture the materials and construct the facilities (Figure 1).[22] (The hydrogen produced by electrolysis also has a much lower EROI than the electricity generated by non-dispatchable wind and solar energy.)
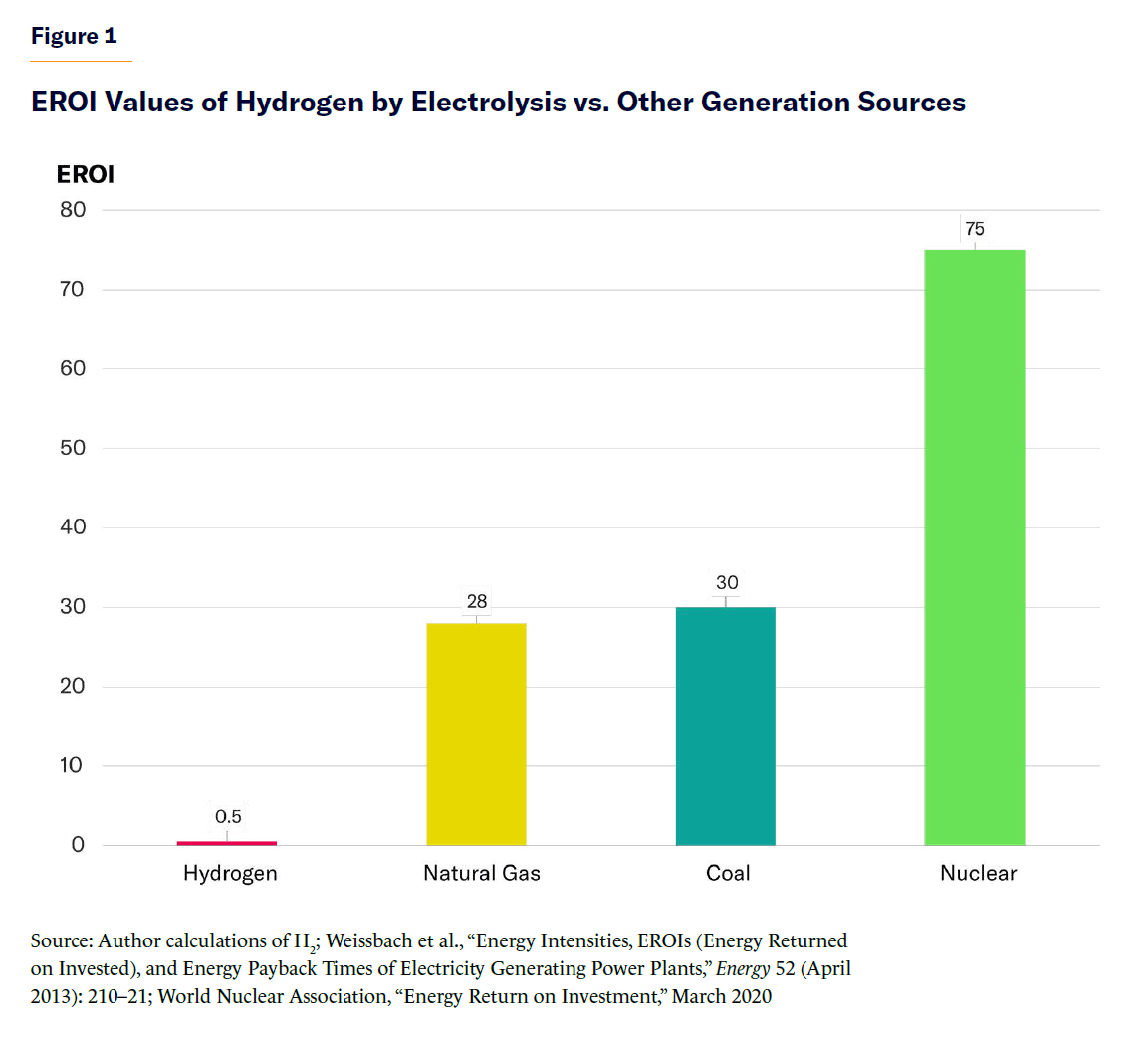
Ignoring the potential economic value (discussed next) of energy storage—such as pumped hydroelectric plants that use cheap electricity produced when demand is low to fill a reservoir that can then generate high-value electricity when demand peaks—energy resources with EROI values of less than one have no economic value. Just as no one would agree to spend $100 on an investment with a negative return, it is foolish for society to invest in any energy resource that inherently requires more energy to produce than it can provide.[23]
Hydrogen as an Energy Storage Medium
In addition to its value as a carbon-free resource, there is another potential counterargument to evaluating the economics of green hydrogen that is based solely on its EROI: hydrogen can be used as an energy storage medium, similar to a battery. Thus, intermittent wind and solar energy could be used to manufacture hydrogen, which could then be used when and where needed, much as batteries are envisioned to store wind- and solar-generated electricity. This is not the stated purpose of the administration’s plan to build hydrogen hubs and use the hydrogen manufactured as a substitute fuel in industrial applications; nevertheless, using hydrogen to store and release energy similar to a pumped storage facility (like a hydroelectric dam) might have positive economic value if the cost of manufacturing and storing the hydrogen is less than its economic value when it is used.
This raises two questions. First, is green hydrogen a more efficient and less costly way to store energy for future use than a battery or other energy storage technology? Second, is the value of energy stored using green hydrogen greater than the cost?
The answers to these questions are complex, particularly because there are different types of batteries and different purposes for storing energy. A similar concept to EROI is called energy stored on invested energy (ESOI), which compares the amount of energy required to store a given quantity of energy. Unlike EROI values, ESOI values are always less than one, because not all stored energy can be recovered. Consequently, stored energy is often called “net energy.” One net-energy analysis found that the ESOI for hydrogen was higher than that of a lithium-ion battery.[24] Another analysis found that hydrogen storage and batteries should be viewed as complements, rather than substitutes, with hydrogen better suited for long-term storage but batteries better suited for small and short-term applications, such as mobile phones.[25]
Fossil fuels, water behind hydroelectric storage dams, and uranium all store energy. Fossil fuels are easily transported and can be used directly or used to generate electricity. Water and uranium can be converted to electricity. The need for storing vast quantities of hydrogen or electricity in batteries is a consequence of policies to promote and subsidize intermittent wind and solar power, along with policies to promote and subsidize electrification of the U.S. economy. Today, the U.S. still relies primarily on fossil fuels and nuclear power, which obviates the need for battery storage systems and stored hydrogen to provide energy and electricity.
A broader policy question is whether creating an underlying need for storing energy needed to compensate for increased reliance on intermittent wind and solar power is economically rational.[26] A complete discussion of that topic is beyond the scope of this Issue Brief. To address the issue, one would need to perform a benefit-cost analysis that compared the costs of storage (batteries, hydrogen, etc.) needed to compensate for wind and solar power’s inherent intermittency against the cost of low- or zero-carbon electricity from generating resources—such as natural gas and nuclear power—that can be dispatched when needed.
Green Hydrogen Production Costs and the Feasibility of the Energy Department’s “Earthshot” Goal
The U.S. Department of Energy’s Hydrogen Earthshot program is pursuing two paths for low-cost hydrogen: (1) manufacturing hydrogen with natural gas and capturing the resulting CO2 emissions; and (2) manufacturing hydrogen using electrolysis and surplus electricity generated from zero-carbon wind and solar generation. Barring the invention and commercialization of a new technology by 2030 that fundamentally alters how hydrogen is produced, this Issue Brief concludes that manufacturing 10 million metric tons of green hydrogen for $1/kg is unrealistic, regardless of the path. Here are the numbers:
Green Hydrogen Production: Natural Gas Reforming
A December 2023 report by the National Energy Technology Laboratory (NETL 2023) discusses pathways toward $1/kg hydrogen using steam methane reforming (SMR) and advanced methane reforming (AMR) technologies.[27] The report begins with an assumed 2023 baseline levelized cost for the two technologies,[28] including carbon capture, storage, and transport of $1.69/kg of hydrogen for SMR and $1.64/kg for AMR. Importantly, these costs do not appear to be based on existing facilities because, in the U.S., there is only one operating SMR plant with carbon capture. That plant is operated by Air Products and Chemicals, Inc. and is located within an oil refinery in Port Arthur, Louisiana. However, no cost data are publicly available for that plant.[29]
Of these values, about half represents the cost of the natural gas used: $0.85/kg for the former and $0.80/kg for the latter.[30] A breakdown of the remaining costs shows a levelized capital cost for the assumed SMR plant as $0.34/kg (2020$), $0.40/kg for fixed and variable operating costs, and $0.10/kg levelized cost to capture, transport, and store the carbon produced. Almost half the capital costs, 46%, are for carbon capture. Although carbon capture proponents claim that those costs will decline by 75%,[31] a more recent analysis by the International Institute for Sustainable Development suggests that such predictions are far too optimistic.[32]
Moreover, a review of the assumptions used in NETL 2023 to calculate levelized costs shows them to be unrealistic.[33] For example, the report assumes a cost of debt of 7.25%, a cost of equity of 5.16%, and a weighted average cost of capital (WACC) of 5.96%. The WACC value is a fundamental input to levelized cost calculations. However, a review of the 2019 source document[34] for NETL 2023’s assumptions shows that the authors have made a significant error. Specifically, the source document, which was prepared before the subsequent increase in interest rates, uses a cost of debt value of 5.0% and a cost of equity of 10.0%, with an overall WACC of 7.25%.
Because debt holders have a senior claim to a firm’s assets over equity investors, equity investors will always demand a higher expected return that reflects the higher risk of nonpayment. Moreover, for a new technology, a cost of equity of 10% is likely far too low, as that rate is more in line with current allowed equity returns for regulated electric utilities.
The NETL 2023 report also assumes a 30-year lifetime for SMR and AMR plants. However, other recent studies assume a 20-year lifetime for an SMR plant, with or without carbon capture.[35] Using the 7.5% WACC in the 2019 source document and 20-year assumed life increases the reported levelized cost by 33%. Using a WACC of 10% increases the levelized capital cost by 62%.
The NETL “pathways” to $1/kg hydrogen assume that improved technology can reduce capital and operating costs by about one-third by 2030. For SMR plants, the single largest cost reduction is the assumed sale of captured carbon, most of which today is (perhaps ironically) used for enhanced oil recovery. For AMR plants, the largest cost reduction that the NETL assumes is from the sale of argon, which is produced as a by-product.
Nevertheless, given the erroneous levelized cost calculations, even these assumed cost-reducing factors will not achieve the $1/kg goal. Of course, it is possible that financing costs could decrease significantly, although increasing U.S. deficits render that unlikely. It is also possible that technological breakthroughs could reduce SMR and AMR costs more than projected. But it is unlikely that such breakthroughs will be discovered—and, more importantly, commercialized—in the next six years. Not only are new technologies not developed on a made-to-order, legislative timetable, but efforts to commercialize technologies typically take many years.
Green Hydrogen Production: Electrolysis
Carbon capture cannot remove 100% of the CO2 produced by reforming natural gas; therefore electrolysis, using emissions-free wind- and solar-generated electricity, is the more touted technology. But if all the relevant costs are included—the cost of the electrolysis facilities themselves; the cost of the electricity from wind and solar generators needed to produce hydrogen; the cost of transmitting that electricity to electrolysis facilities from those wind and solar generators; the cost of backup battery storage to compensate for the intermittency of wind and solar energy; and the cost to compress the hydrogen that is manufactured—the Earthshot goal of producing green hydrogen at $1/kg cannot be achieved. Here are the components:
Plant Costs
If all electrolysis facilities operated around the clock, the total installed electric capacity needed to produce and compress 10 million metric tons of hydrogen per year, assuming an electric requirement of 51 kWh/kg of hydrogen (the sum of the low electrolysis and compression values in Table 1), would be more than 58,000 MW.[36] Currently, the average cost of an electrolysis facility is estimated to be $1,000–$1,500 per kW of capacity.[37] Even if this cost range decreases by 80%, to between $200/kW and $300/kW, despite inflation, the resulting capital cost would be $11.6 billion–$17.4 billion, excluding financing costs. Assuming an electrolysis facility lifetime of 27 years, which would include replacing the “stack”—basically a membrane separating an anode and a cathode that is electrically charged, which causes a chemical reaction that splits water into its components used to produce the hydrogen twice[38]—the resulting levelized capital cost, including financing, would be approximately $0.11/kg of hydrogen produced.[39]
Ongoing maintenance costs for electrolysis facilities have been estimated to be about $40/kW-year or $2.44 billion annually.[40] For 10 million metric tons of hydrogen, this is equivalent to $0.23/kg. If we assume that advances in production technology reduce maintenance costs by half, a reasonable lower-bound maintenance cost is about $0.12/kg. Thus, electrolysis plant capital and maintenance costs will total at least $0.23/kg.
Other costs for hydrogen manufactured by electrolysis include:
Electricity Generation
As experience in California demonstrates, the market price of electricity can fall below zero in some hours when the quantity of electricity supplied is greater than demand. Nevertheless, the costs to build and maintain the wind and solar generating capacity still exist and must be accounted for.
Thus, even if, as assumed previously, sufficient additional wind- and solar-power capacity is constructed—such that the output is devoted solely to hydrogen production—the owners of those facilities must recover the costs of constructing and operating them. They may sell the electricity generated into wholesale power markets at the contemporaneous market price, called the “spot” market price. They may, instead, sign long-term contracts with buyers. But in the long run, they cannot sell electricity at prices that fail to recover the capital and operating costs of the facilities.
According to the U.S. Energy Information Administration (EIA), the levelized costs of solar and wind generation, excluding federal tax credits, are about $35/MWh and $40/MWh, or $0.035/kWh and $0.04/kWh, respectively, in 2022$.[41] Consequently, the cost of the electricity needed to produce and compress green hydrogen at electrolysis plants will be about $2.00/kg.[42] Given the increasing costs of materials needed to manufacture wind turbines and solar cells, it seems unlikely that these costs will decrease. Moreover, financing costs have increased because interest rates have returned to more normal levels, rather than the low rates that had persisted since the 2008 financial crisis.
Electricity Storage
No electrolysis facility could be expected to operate only when intermittent supplies of “surplus” electricity were available. Given the average availability of wind and solar power facilities in the U.S.,[43] such a facility would be expected to operate only about one-third of the year. Moreover, it would be impractical and uneconomic to require employees to be “on call” whenever sufficient wind and solar generation were available and to be idle when there was not enough generation.
To ensure reliable supplies of electricity to electrolysis facilities when wind and solar generation is not available, electrolysis facilities would require backup capacity, using either battery storage or DEFRs burning that same green hydrogen. The latter would be an obvious net-energy loser, as it would require far more hydrogen to fuel the DEFRs than would be produced by the electrolysis facilities themselves. Hence, facilities to manufacture green hydrogen by electrolysis would require battery storage to operate continuously. Typical utility-scale battery storage facilities are designed to provide four hours of backup for each unit of capacity. For example, a 100 MW battery storage facility is designed to provide up to 400 MWh of electricity. In practical use, battery storage is never drained below 20% capacity, as this reduces battery life, which implies that a 400 MWh storage facility would supply only 320 MWh.
In 2022, the average cost of a typical, four-hour battery storage system was estimated to be $446/MWh (2021$), based on a 60 MW battery capacity.[44] According to EIA, the levelized cost of battery storage placed into service in 2028 will average about $130/MWh, or $0.13/kWh.[45] Even if technological advancements reduce the 2028 EIA estimate by half, the levelized battery storage costs per kg of green hydrogen would be about $3.50 for 48 hours of battery storage capability and $0.875 for 12 hours.[46]
In addition, the electricity generated by wind and solar power will need to be transported to the electrolysis facilities themselves. According to EIA, the average cost of electricity transmission alone (ignoring local distribution costs) ranges between $0.01 and $0.04/kWh.[47] Thus, simply transmitting the necessary electricity would cost between $0.54/kg and $2.16/kg. Furthermore, accommodating the increase in wind and solar generation needed to provide electricity for green hydrogen production will require doubling the transmission grid, which will increase electric transmission costs.
The transmission costs do not include the costs associated with electric utilities’ local distribution networks. Those costs are higher still, between $0.04/kWh and $0.06/kWh.[48] Presumably, therefore, no electrolysis plants would be connected to any local utility distribution network. Instead, the plants would need to be connected directly to the high-voltage transmission grid, much as aluminum smelters in the Pacific Northwest were decades ago.
Compression and Storage
Because hydrogen’s density is so low, it must be compressed to be usable. (It must also be compressed to be transported economically.) Alternatively, hydrogen can be liquefied for transport. In either case, the largest cost is for the compressors themselves, plus the electricity required to operate the compressors and maintain cooling in storage containers. Compression is a mature technology, and the energy required to compress hydrogen is a function of hydrogen’s density. Hence, it is unlikely that there will be major technological advances that significantly improve compressor efficiency and reduce costs.
Based on 2 kWh–6 kWh of electricity needed to compress each kg of hydrogen and the estimated levelized cost of wind and solar power, compression costs range between $0.08/kg and $0.24/kg.
Summary of Green Hydrogen Production Costs
In total, even under highly optimistic assumptions, the actual cost to produce green hydrogen is unlikely to fall much below $3/kg, even when needed battery storage costs to overcome wind and solar intermittency are excluded. When that cost is included, the cost to produce green hydrogen increases to $3.62/kg–$8.85/kg (Table 2).
Table 2
Summary of Green Hydrogen Production Costs
Line No. | Item | Cost $/kg of H2 | |
Low | High | ||
1 | Electrolysis Facility Capital Cost ($200/kW–$1,000/kW) | $0.11 | $0.55 |
2 | Fixed Operation and Maintenance Costs ($/kg) | $0.12 | $0.24 |
3 | Wind and Solar Cost ($0.04/ kWh, unsubsidized) | $1.89 | $2.16 |
4 | Transmission Cost ($0.01/ kWh–$0.04/kWh) | $0.54 | $2.16 |
5 | Hydrogen Compression Cost (2 kWh–6 kWh) | $0.08 | $0.24 |
6 | Subtotal (Lines 1–5), Assuming No Battery Storage Costs | $2.74 | $5.35 |
7 | Battery Storage Cost ($0.13/kWh, unsubsidized, 12–48 hours) | $0.88 | $3.50 |
8 | Total with Battery Storage | $3.62 | $8.85 |
The low-end values for the electrolysis facility capital and maintenance costs, plus the costs to transmit electricity to those facilities (lines 1, 2, and 4) total $0.77/kg. Hence, to meet the $1/kg goal, the cost of the electricity needed would need to be, at most, $0.23/kg (excluding the costs for any battery storage and all compression costs). Even assuming a technological advance in electrolysis efficiency to 95% from 80%, which would reduce the electricity needed to 42 kWh/kg of hydrogen from 49 kWh, the average cost of electricity would have to be about one-half of one cent per kWh ($5.00/MWh). However, that is about 20% of the unsubsidized levelized cost of wind and solar power. Operation and maintenance costs alone for onshore wind turbines are about $0.011/kWh ($11/MWh).[49] Even maintenance costs for solar photovoltaic systems are higher than the maximum electricity cost needed to meet the U.S. Department of Energy’s Earthshot goal—$1/kg production.[50]
Finally, the hydrogen produced must be transported to facilities where it will be used. This will entail yet more costs unless those facilities are co-located with electrolysis plants. Current estimates are $2.3 million–$4.5 million per kilometer (km) to build a hydrogen pipeline, depending on its size.[51] For example, the planned 53,000 km European hydrogen “backbone,” which calls for repurposing 30,000 km of existing natural gas pipelines and building over 20,000 km of new hydrogen pipelines, has an estimated cost of $80 billion–$140 billion.[52] One estimate for the cost of transporting hydrogen in a 1,000 km pipeline is about $0.50/kg.[53] (The government’s $1/kg goal ignores transportation costs.)
Green Hydrogen’s Negligible Impact on Carbon Emissions
As a result of these expenditures and government subsidies, the administration hopes to reduce CO2 emissions by 25 million metric tons annually by 2030. By comparison, in 2022, U.S. energy-related CO2 emissions totaled just over 4.8 billion metric tons, and world energy-related CO2 emissions totaled about 34.4 billion metric tons.[54] Thus, the administration’s goal represents less than two days’ of this country’s 2022 CO2 emissions and just six hours of world emissions. Such a reduction would have no measurable impact on world climate, especially as emissions from China and India continue to increase rapidly.
The implied costs of CO2 emissions reductions associated with the Clean Hydrogen Strategy, which calls for manufacturing 10 million metric tons of green hydrogen per year by 2030—also are much greater than estimates of the social cost of carbon (SCC). In other words, the cost to achieve the projected CO2 reductions from substituting green hydrogen in industrial applications is greater than the estimated value using the SCC.
Green hydrogen is most likely to replace natural gas as a feedstock for industrial manufacturing applications (e.g., cement) because coal is rarely used as an energy resource in those applications. In 2022, non-electricity-producing industrial plants consumed about 42 million tons of coal, less than 10% of total U.S. coal consumption. The energy content of the coal consumed was about 845 trillion Btus (TBtus).[55] By contrast, the industrial-sector consumption of natural gas, excluding consumption in industrial cogeneration facilities that produce electricity, was 8,537 TBtus, 10 times larger.[56]
Consider: 1 kg of natural gas produces 2.75 kg of CO2 when burned. However, the heat content of natural gas per kg is about 35% that of hydrogen. In other words, burning 1 kg of hydrogen produces as much energy as burning just under 3 kg of natural gas. Thus, burning 1 kg of green hydrogen manufactured using only emissions-free electricity (i.e., generated from wind and solar power) would avoid about 7.9 kg of CO2[57]
The $3/kg subsidy for green hydrogen offered under IRA is thus equivalent to a price of $375/metric ton of CO2,[58] whereas the current SCC value is $51/metric ton. (The administration has proposed raising that value to $191/metric ton.)[59] Thus, the green hydrogen subsidy substantially overvalues CO2 reductions.
The effective CO2 reduction cost also can be estimated based on the difference between the average market price of natural gas and the estimated production cost of green hydrogen, excluding the costs of transportation to industrial end-use locations. The average market price of natural gas at Henry Hub in southern Louisiana, which is the most common pricing point for natural gas, was $2.53 per million Btus (MMBtus) in 2023. Based on an average heat content for natural gas of approximately 40,000 Btus/kg, the average price is equivalent to about $0.10/kg.
Using the optimistic estimate of green hydrogen production cost of $2.74/kg from Table 2 (excluding all battery storage costs that would enable an electrolysis plant to operate on a regular schedule), the difference in costs between natural gas and green hydrogen is $2.64/kg. Hence, if 1 kg of green hydrogen avoids 7.86 kg of CO2 from natural gas, the avoided CO2 cost is about $340 per metric ton.[60] If minimal battery storage costs are included, raising the cost of green hydrogen to the $3.62/kg value shown in Table 2, the cost difference between natural gas and green hydrogen increases to $3.51/kg and the resulting avoided CO2 cost increases to $447 per metric ton, more than double the $191 SCC price proposed by the Biden administration and 800% higher than the current $51 per metric ton price.
Since 2000, the highest average annual Henry Hub price for natural gas was $8.86/MMBtus (in 2008). Even at that historically high price, which is equivalent to about $0.35/kg, the difference in costs between natural gas and hydrogen would be at least $2.39/kg, and the avoided CO2 cost would be about $305/metric ton. To reach the current SCC value of $51/metric ton, the average price of natural gas would have to increase to $2.36/kg or $59/MMBtu.
Conclusion
As this Issue Brief has shown, the stated goal of producing green hydrogen at a cost of just $1/kg is unrealistic, even assuming large gains in the efficiency and reductions in costs of electrolyzers. The claim that surplus wind and solar energy will be available to produce this hydrogen ignores basic economic principles. Not only would huge quantities of new wind and solar capacity have to be built, but the increased demand for electricity—caused by the amount of hydrogen production envisioned by the Biden administration’s Clean Hydrogen Project—would raise wholesale electricity prices. Including the costs of transmitting electricity to electrolysis facilities, as well as the costs of compressing and storing the hydrogen that is produced, raises the costs still further. Unless electrolysis facilities were operated only when surplus wind and solar power was available, and sat idle otherwise, large quantities of battery storage will be needed to enable those facilities to operate, if not around the clock, at least on a regular schedule.
More fundamentally, hydrogen, green or otherwise, is not a useful dispatchable energy resource because it requires more energy to produce than it can provide. That is an immutable thermodynamic fact. Barring the discovery of large quantities of elemental hydrogen on earth that can be extracted at low cost, it simply makes no sense to develop such net-energy sinks, whether or not they are “emissions-free.”
The contribution of hydrogen to the reduction of CO2 emissions will be negligible and have no measurable impact on world climate. Moreover, the cost per ton of reduced CO2 far exceeds estimates of the social cost of carbon, meaning that the cost of carbon reductions exceeds the value of those reductions. Hence, pursuing green hydrogen production, regardless of its EROI, to reduce CO2 emissions makes no economic sense.
Given these facts, the ineluctable conclusion is that all hydrogen-related subsidies are best abandoned. Instead, the focus should be on streamlining the process for licensing new nuclear plants—especially, small, modular ones—and investing in research and development efforts to reduce the cost of those nuclear plants. These plants will be scalable, will not require costly backup and storage, and can be sited near load centers, thus avoiding costly transmission system upgrades. Finally, in addition to producing emissions-free electricity, nuclear plants have the highest EROI values of any existing energy resource, a critical factor if the world’s increasing demand for energy is to be met cost-effectively.
Endnotes
Photo: audioundwerbung/iStock
Are you interested in supporting the Manhattan Institute’s public-interest research and journalism? As a 501(c)(3) nonprofit, donations in support of MI and its scholars’ work are fully tax-deductible as provided by law (EIN #13-2912529).